如何实现钢铁冶金流程复杂固废资源化循环利用?
我国是全球最大的钢铁生产国和消费国,由于我国资源禀赋的原因,支撑我国大规模钢铁生产的主要是以高炉、转炉为主的长流程钢铁企业,全国钢铁行业每年产生的固体废弃物超过6亿吨,其中渣类固废基本已通过水泥、建材行业进行消纳,还有部分固废含有铁、碳等有价元素,因赋存了Zn、K、Na、Cl、S及高挥发分有机物,不能直接在钢铁流程循环利用,成为了难处理的复杂固废,尤其是危险废物,给钢铁工业造成了资源浪费和环境破坏,阻碍了我国钢铁工业高质量发展。因此,必须针对钢铁系统的多源复杂固废制定一个全方位的低碳、低污染、低成本资源化处置技术方案。
中冶长天国际工程有限责任公司、国家烧结球团装备系统工程技术研究中心叶恒棣团队与中南大学、宝钢股份、山东永锋钢铁等企业和高校共同努力,对钢铁流程复杂固废中质能迁移、转化、循环利用规律进行了系统而深入的研究,取得了许多有价值的研究成果,不仅实现了钢铁企业厂内固废不出厂,还可以协同消纳部分社会废弃物,提升了钢铁企业的功能价值和社会价值。
一、钢铁冶金流程固废物化特征及循环利用准则
钢铁全流程固废的成分复杂,物理和化学性质各不相同。按照固废的来源划分,钢铁流程固废可分为烧结固废、焦化固废、炼铁固废、炼钢固废等;按照物理特征划分,也可以分为渣类固废、尘泥类固废和有机杂物类固废。
钢铁流程固废的主要特征如图1所示。
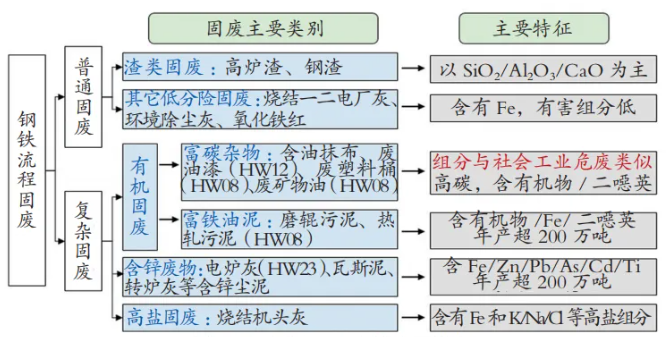
图1 钢铁流程固废的主要特征
冶金流程的许多固废都含有铁、碳等钢铁流程需要的元素。如果能将富铁、碳固废中的毒害物质从固废中分离出去,有价资源就有可能被钢铁主流程循环利用,分离出来的毒害元素可与钢铁主流程协同进行污染物治理。
按照价值极大化原则,固废处置的价值优先级顺序应当为:物质利用>能源利用>无害化处置。如图2所示,对于具有物质属性的固废,必须优先对其进行资源循环利用;对具有能源属性的固废,可以优先将其用作工业生产的燃料;对仅具有毒害属性的固废,则尽量把毒害属性转变为物质、能源属性,最后的措施才是对其无害化处置。
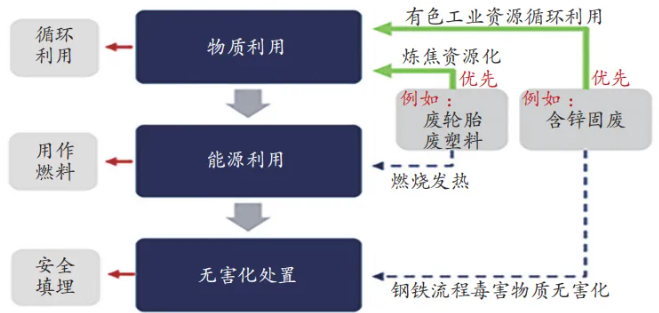
图2 质能价值优化循环利用原则
钢铁流程产生的废弃物相态可分为气态、固态和液态,但是废弃物的相态不是固定的,在治理过程中会发生转化,污染物会在不同相态之间迁移。因此,冶金流程固废的处置必须关注污染物的迁移,消除二次污染的风险。同时,要对固废组分分离过程产生的多相流与钢铁主流程对口协同,实现固废梯次处置、物穷其用。
基于价值极大化原则,固废的高值资源化处置必须要把矿山与冶金、钢铁与有色、钢铁与化工、钢铁与城市进行生态链接,构建多行业、跨领域之间深度耦合新理念,实现跨领域原料互供、固废协同处置。
二、钢铁冶金流程有机固废热解-焚烧工艺技术及装备
有机固废有价组分主要包括固定碳和铁等,在铁、碳资源循环回用过程中,必须要先经过组分分离,把有机固废中的挥发分、二噁英去除至满足冶金炉窑入炉的要求,其整体技术路线如图3所示。钢铁流程的有机固废经过控温热解以后,部分挥发分进入未燃尽的热解焚烧气,具有一定热值,可以作为低热值的冶金副产煤气向烧结、热风炉等冶金炉窑供能,也可以配备专门的二燃室,在二燃室中充分燃烧,再通过余热锅炉回收热量。控温热解产生的高温渣在低氧或氮气保护气氛下采用水冷间接冷却,以保留渣中固定碳和金属铁组分。热解渣中保留的固定碳组分可作为钢铁流程的还原剂或燃料进行回收利用;铁则以金属铁或氧化铁形式作为铁原料返回钢铁流程回收利用。
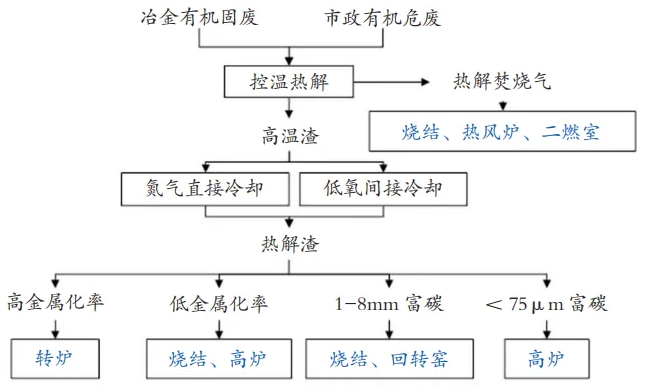
图3 有机固废资源循环利用整体技术路线
热解反应器是热解-焚烧工艺最关键、最核心的装备。目前,市场上热解工艺所使用的基本炉型主要包括:流化床、回转窑、移动床、固定床等。钢铁流程的有机固废最大的特征是来源广泛、组分繁杂,结合热解-焚烧工艺技术原理,综合比较目前几种典型的热解炉来看,采用内热式回转窑将较好地解决有机固废来源广泛、成分复杂、尺寸各异的问题,物料在回转窑内翻滚实现均匀受热,回转窑内通过控制合理的空气输入对部分废弃物进行氧化,提供自身热解所需要的热量,实现了自身能量平衡。为了进料、进风及辅助燃烧器的布置简便,操作维护方便,有机固废热解焚烧窑采用顺流运行模式。
三、回转窑法脱锌工艺流程及关键装备
含锌含铁固废铁、锌高效还原分离的工艺路线如图4所示。配料时应采用高碱度物料方针。含锌含铁固废与还原剂混匀后造球,造球方式可采用圆盘造球或强力扰动造球,为提高球团质量推荐选择强力扰动造球方式。球团碳含量为10%~20%,对于脱锌渣作为烧结原料循环利用时,应控制复合球团粒度为3~8mm;对于脱锌渣作为转炉原料循环利用时,应控制复合球团粒度为8~15mm。复合球团经多场协同可控回转窑还原,还原高温段温度范围为1000~1150℃,物料在高温段停留时间不少于35min,含铁组分在回转窑内还原为金属铁,高温渣从窑头排出后经干式冷却,冷却介质宜用氮气,获得高金属化率产品作为转炉炼钢原料,低金属化率产品进入烧结配料;锌进入烟尘经除尘后收集成为次氧化锌产品,尾气经余热回收、烟气净化后排放。

图4 含锌含铁固废铁、锌高效还原分离的工艺路线
含锌含铁固废制备成球团为还原过程锌铁颗粒表面与还原气体之间营造良好的传热传质条件,高强度的球团在回转窑运转过程中不易产生大量粉末,加重结圈现象。因此,含锌含铁固废需与还原剂进行混匀后制备高强度球团。造球方式可采用圆盘造球或扰动造球方式。为实现含锌含铁固废铁、锌高效还原分离,又不出现严重的结圈现象,需要对还原过程的温度场和气氛场进行准确控制,窑内氧气分布不能出现局部过量富集,以防造成局部高温或氧化气氛过剩。多场协同可控回转窑技术原理如图5所示。
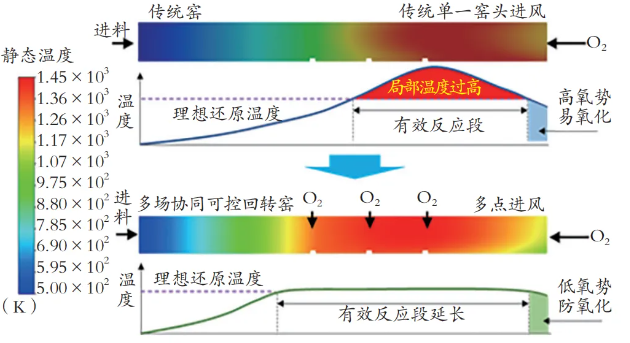
图5 多场协同可控回转窑还原技术原理
四、多金属高盐固-液废物协同资源化技术
高盐固废水洗脱盐过程虽可实现铁-盐的高效分离,但在水洗过程中包括Ca、SO42-及重金属铊均会溶出,造成水洗液中杂质含量较高,除重除硬成本较高。研究表明,在高盐体系下进行酸性水洗时,由于高盐固废中部分可溶出组分对铊溶出的抑制作用,可有效降低铊在水洗过程的污染扩散。故水洗过程采用两段水洗技术流程,先通过一段高盐酸性废水水洗,实现盐选择性分离,得到低铊浓盐水,再通过低盐酸性废水对一段水洗滤饼进行二次水洗,实现铁和铊的高效分离。经两段酸性水洗后,可得到低铊高盐水用于回收盐资源,产生的富铁滤饼可返回烧结工序对铁资源进行回收,二级洗涤产生的低盐富铊液还为铊的富集和资源化提供了途径。
高盐固废经洗灰后所得低盐低铊富铁料中含有丰富的铁资源,铁品位可稳定超过40%,是一种较好的炼铁资源,可直接返回烧结工序进行利用。部分企业的机头灰中银含量也较高,在水洗过程也会富集在富铁料中,具有回收价值。此外,在“固废不出厂”的要求下,除重除硬过程产生的含铊污泥中会富集少量重金属,也可通过烧结工序进行消纳。
五、跨领域多源固废协同资源化组合方案及智慧平台构建
高炉灰、转炉灰和电炉灰还原脱锌时需要消耗碳作为还原剂和燃料,炼钢灰中碳含量极低,铁含量高,为了实现炼钢灰中锌的有效脱除,必然需要配加较多含碳高的高炉灰或额外配煤,导致回转窑处理量大、处理能力和能量浪费,且原料铁含量高又导致回转窑易结圈的隐患,因此提出了利用钢铁流程废水,将湿法高盐固废处置和火法还原脱锌协同起来,组成湿/火法组合选冶方案,提前将含锌粉尘中的锌铁组分进行初步分离,可以减少回转窑处理量,提高还原效率,降低能耗。同时,利用钢铁厂内废水进行含锌粉尘的磨选处理和烧结灰水洗,不额外使用新水,做到了厂内废水的多级循环利用。
冶金复杂固废预处理时,通常会产生多种相态的副产物,不同相态的副产物以不同方式与烧结流程重新耦合。有机固废经热解渣可以掺入烧结或与含锌固废混匀,减少外配焦炭的使用,达到“以废代碳”。含铁尘泥和高盐固废预处理渣掺入烧结中可以回收其中的铁资源,实现“以废代铁”,还可以将固废火法处置产生的烟气并入烧结烟气协同净化,将冶金流程的酸性废水调质后可以用于高盐固废水洗,节约生产成本。
除了烧结外,钢铁流程的其他工业窑炉也具有高价值协同处置固废的潜力。高炉对铁原料和焦炭的粒度和强度都有一定的要求,经预处理后的固废铁品位、颗粒粒度、强度满足高炉炼铁要求,可以作为铁原料加入高炉。富铁的固废经过还原后,有可能获得较高金属化率的含铁渣,直接进入转炉炼钢可以缩短固废在钢铁流程的处置工序,降低能耗和碳排放。
当前,固废产量大、来源广、成分极其复杂。固废协同处置设施的工艺流程物质流、能量流差别很大,对入炉固废也有着不同的要求。而固废属性与工业流程有着优选的生态化适配路径,特定的固废只有进入最合适的工业窑炉进行协同处置,才能最大程度发挥协同处置的资源利用效益。因此,提出了构建区域性固废协同处置智慧网络平台的构想。依托5G模块化数据采集技术、云服务技术等现代化信息手段,智慧平台不断采集固废基础数据,智能仓储实时反映固废产量和堆存信息,通过云计算匹配经济和环境效益最优的协同处置路径,固废通过物流送往目的设施进行协同处置。通过北斗-物联网技术实现固废溯源和物流追踪,采用实景三维和视景仿真技术,实现固废从产生、检测、储存、运输到最后处置的过程可以通过智慧平台进行全流程可视化展示、运行管理和监测,有效促进固废在区域内的协同高效处置。
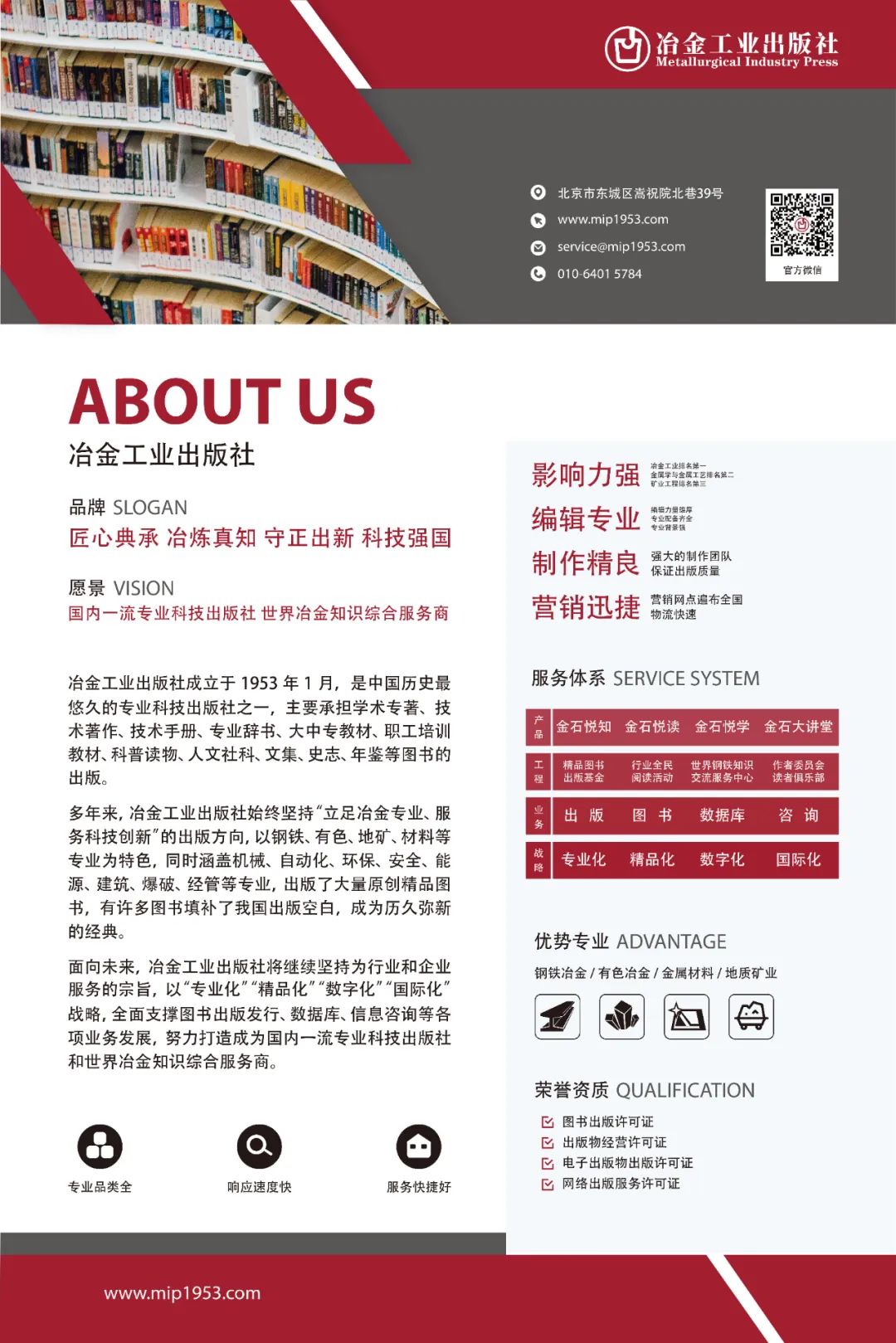